Bleeding Pallets? 6 Things to Do Now.
- Brenda Gallagher
- Mar 21, 2018
- 3 min read
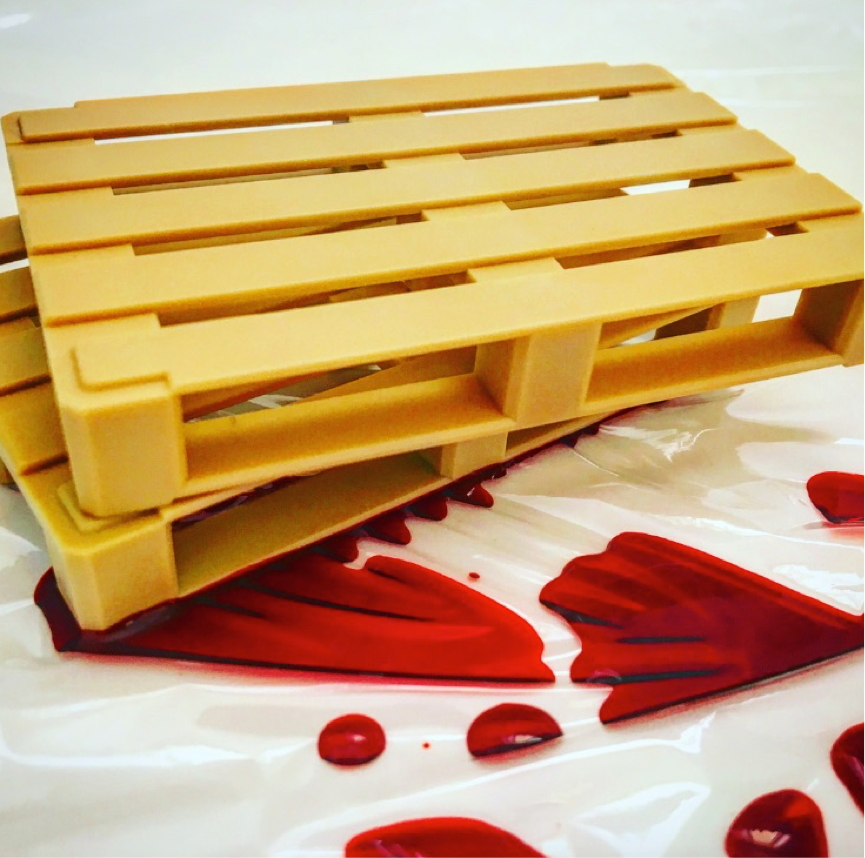
I hate pallets with a passion. It’s not the day-to-day pallet management that I hate; hell, it’s not even the pallet companies’ compensation costs or daily hire charges that get to me.
What is frustrating is when companies don’t treat pallets like the inventory item that they are. They look at you, shocked and surprised, wondering how they have lost hundreds of thousands of dollars worth of pallets and expect a magic wand to be waved and voila!, they haven’t wiped all that money from their bottom line.
In trouble with pallets? Here’s a how-to in what to do now.
1. Accept the fact that you are not going to recover all the pallets that you have lost.
This can be a big leap, as you may not have even realised that you were in deficit. It can be a shock to the system! Factors such as how long the losses have been going on, the integrity of your paperwork and the physical security of your site will affect how much you can recover.
I am not saying to just accept these losses without a fight; rather, treat any pallets recovered as a bonus against previous mismanagement.
2. Talk with your pallet provider(s).
Gone are the days of pallet companies saying, “Too bad, so sad” and wiping their hands of the problem. Both Chep and Loscam want to help companies as much as they are able, to fix historical issues and give free training, tips and tools to prevent a reoccurrence of the current predicament. Worst case, Chep and Loscam will provide compensation packages to pay out the lost pallets on your account – either as one bulk payment or in instalments.
3. Engage a professional pallet investigator / company.
Once a pallet loss has been identified, time is of the essence. Depending on the relationship that you have with each of your trading partners, there is a limited window of opportunity in which you will be able to recover the pallets and hopefully, the rental costs. You cannot dilly-dally.
There will be reasons that your company has lost pallets and I guarantee that skills and resourcing will have played a part. Let your team do their day jobs and let the pallet investigator do theirs – who knows, the pallets that are recovered may offset their costs.
You can also use their expertise to work out strategies to prevent further, ongoing losses.
4. Time to Implement Processes
For the good of your bottom line, implement some processes. Examples include:
Limit access to perform transfers, dehires, etc to select Team Members with individual log-ons
Monitoring and handling of corrections and rejections
Prevention of double transfers from both suppliers and transport companies
Stopping pallet exchanges and transfers for the same movement
Reconciliation of your account
Stocktakes
5. Site Security
You can have the best processes in the world but if there is unauthorised access your site to take pallets, you could have a problem. Don’t assume that because your site is secure and you have a gatehouse that you can be complacent: one such site lost a truckload of pallets over Christmas by a driver masquerading as the transport company picking up dehires.
6. Training
Your Team may not realise that pallets are more than just convenient pieces of wood or plastic on which to pack and transport your goods on. Train them on what to do right.
Pallet mismanagement is an indicator of the health and culture of your supply chain. In all likelihood, there was at least one member of your Team who was flagging that pallet management was an issue and it needed to be addressed. This is a great opportunity to understand why and how pallets have been lost and what input your Team can have about other processes that can be improved.